As global manufacturing scales rapidly, new factories grapple with two critical issues when upgrading compressed air systems:
- Skyrocketing Energy Costs
- Traditional multi-compressor setups waste 20–35% energy due to inefficient parallel operation.
- Compressed air systems account for over 20% of total production costs in most factories.
- Supporting Data:
- 2023 Global Industrial Air Compressor Energy Report reveals 60% of factories use oversized, energy-draining systems.
- A 75kW fixed-speed compressor wastes $10,000–15,000/year under partial loads.
- Downtime Risks in 24/7 Production
- Unplanned compressor failures can halt entire production lines, costing manufacturers $260–$500 per minute in high-value industries like automotive and pharmaceuticals.
- Legacy systems struggle to maintain pressure stability (±0.1 bar), causing product defects.
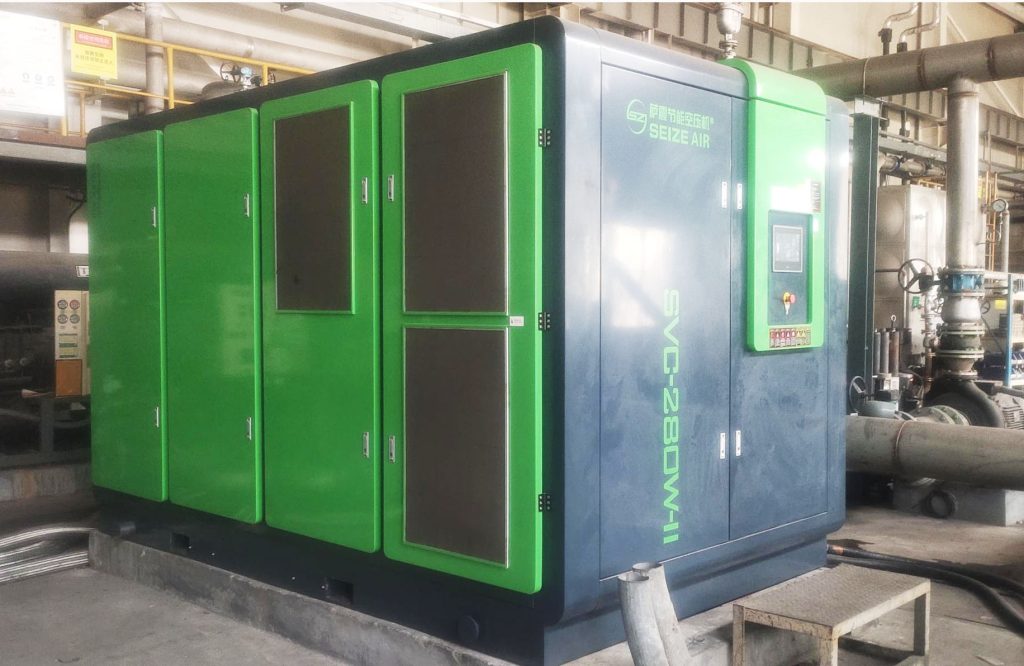
Seize Air’s Permanent Magnet Two-Stage Compressors: 4 Energy-Saving Breakthroughs
1. Pressure Customization Technology | Eliminate Energy Waste
- Tailored Pressure Ranges:
- Low Pressure (3–8 bar): Ideal for packaging, textile, and light assembly.
- Standard Pressure (8–13 bar): Perfect for automotive welding and CNC machining.
- High Pressure (13–40 bar): Designed for PET blow molding and aerospace applications.
- Case Study:
A Chinese automotive parts supplier saved $37,600/year by deploying pressure-zoned Seize Air compressors, reducing idle energy waste by 41%.
2. IE5 Ultra-Premium Efficiency | 30–42% Lower Energy Bills
- Dual-Stage Compression: Achieves 15% higher efficiency than single-stage models by reducing thermal losses.
- Permanent Magnet Motor: Maintains 98% efficiency even at 40% load, versus 70–80% for standard induction motors.
- Smart Variable Speed Drive (VFD): Dynamically adjusts motor RPM to match demand, cutting energy use during low-load periods.
3. Intelligent Multi-Compressor Control | 10–200 m³/min Flow Flexibility
- Cluster Optimization System:
- Automatically activates/deactivates units based on real-time demand.
- Patented airflow balancing algorithm maintains pressure within ±0.01 MPa (±1.45 psi).
- Case Study:
A solar panel manufacturer upgraded to Seize Air’s multi-compressor system, reducing air-related energy costs from 18% to 11% of total expenses ($290,000/year saved).
4. Seize IoT 4.0 Platform | Predictive Maintenance & Remote Control
- 24/7 Performance Monitoring:
- Tracks 20+ parameters (motor current, oil temperature, vibration spectra) via Android/iOS apps.
- Generates automated energy consumption reports.
- AI-Driven Predictive Alerts:
- Detects bearing wear, valve leaks, and filter clogs 48 hours in advance.
- Reduces unplanned downtime by 67% in documented cases.
Factory Expansion Guide: Compressor Selection Strategies
Scenario 1: Small/Medium Factories (50–100 Employees)
- Recommended Setup:
- 22–75kW two-stage VFD compressor + 2–3m³ buffer tank.
- Key Benefits:
- Eliminates frequent start/stop cycles.
- Reduces energy waste during shift changes.
- ROI Analysis:
- Initial investment: $18,000–$60,000.
- Payback period: 2–3 years via energy savings (3-year savings ≈ equipment cost).
Scenario 2: Large-Scale Plants (200+ Employees, 24/7 Operation)
- Recommended Setup:
- 110–250kW two-stage compressors + central controller + heat recovery module.
- Key Benefits:
- Recovers 70–90% of waste heat for water/space heating.
- Centralized control cuts maintenance labor by 35%.
- Verified Results:
A Southeast Asian electronics plant reduced compressor-related downtime by 82% using Seize Air’s smart system.
Technical FAQs: Addressing Global Manufacturers’ Concerns
Q1: Are permanent magnet compressors reliable in high-humidity environments?
A: Seize Air compressors feature IP55 protection and nano-coated components, ensuring stable operation at up to 80% relative humidity. Optional corrosion-resistant packages are available for coastal regions.
Q2: How does two-stage compression improve efficiency?
A: Two-stage systems compress air in two phases with intercooling, reducing discharge temperatures by 28°C (82°F). This minimizes thermal stress and lowers energy use by 12–18%.
Q3: Can Seize Air compressors integrate with existing piping?
A: Yes. Our engineers provide free onsite audits to optimize pipe layouts, minimize pressure drops, and retrofit legacy systems.
Q4: What’s the lifespan of your permanent magnet motors?
A: Designed for 60,000+ hours (7–10 years) with <2% efficiency loss. All motors include a 5-year warranty.
Why Choose Seize Air for Your Factory Expansion?
- Proven ROI: Average 30% energy cost reduction across 1,200+ global installations.
- Turnkey Solutions: Free energy audits, 3D layout simulations, and ROI projections.
- Global Support: 48-hour emergency response, multilingual technical assistance.
Call to Action
Book a FREE Compressed Air Energy Audit today!
- Receive a customized optimization plan within 72 hours.
- Access exclusive factory expansion grants and financing options.